Zebra Printer Won't Print! - Our Top Troubleshoot Tips
- Feb 27, 2018
- 3 min read
Updated: May 17, 2023
Is there anything more frustrating than your label printer going down at a time when you are under pressure to get a job out? As a label printing company we are too familiar with the stress and frustration this causes.
In this blog article we thought we'd share our top tips to rectify the most common faults and issues experienced with zebra label printers. This includes the smaller desktop models such as the Zebra GK420D or Zebra GK420t.

1. Poor Print Quality - the ink smudges or only prints faintly
This is a simple fix but the most common issue we get asked over the phone. The first thing to check is which ribbon and label materials you are using. There are three types of print ribbons: wax, wax-resin and resin. In short, wax ribbons are the cheapest and are only suitable for paper labels whereas resin ribbons are suitable for synthetics (eg. polypropylene or vinyl.)
A wax-resin ribbon is suitable for paper labels or printing onto synthetics when the print doesn't need to be resistant to chemical attack or harsh environments. It is quite common in the workplace for members of staff to inherit printers and not realise the difference between print ribbons available on the market.
If you are using the correct ribbon then the next thing to try is reducing the speed or increasing the temperature of the print head to see if this improves print quality. If the coating of the label material you are printing onto has changed then it could mean the print settings need adjusting to suit. This can generally be changed in the settings window when you click to print.
Ideally you should set the temperature of the printer to the lowest it can achieve satisfactory print quality for your application.
If you aren't sure which printer you have (near edge of flat head) or which ribbons you need to buy to get the best result simply give Crown a call for advice on which type and grade will suit your application and printer.
2. Error Connecting to the Printer
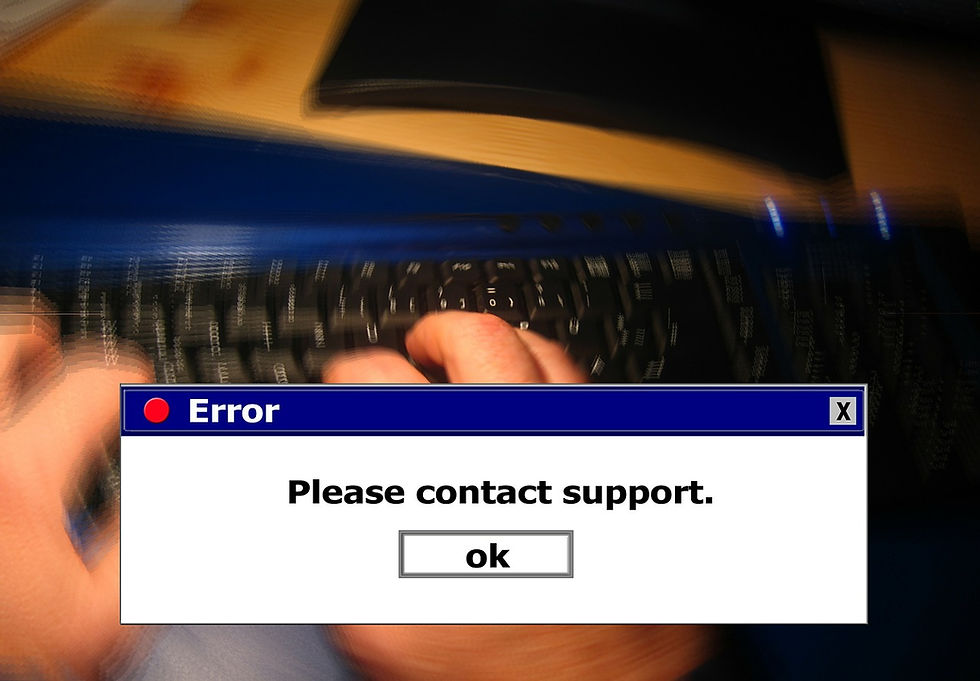
This is a common issue faced when you are setting up a new computer. You may have downloaded the correct label software and hooked up all the cables as you did previously, but the correct printer driver hasn't been downloaded and installed for your Windows operating system.
The manufacturer of the printer should have these driver files available on their website ready for download and installation. Simply google the relevant manufacturer and model number along with 'printer driver' to get hold of the critical files so your PC can communicate with your printer.
3. The Ribbon isn't Transferring onto the Label
Check which way the printer ribbon has been presented - these can be either wound inkside in or inkside out. The configuration depends on the model you are using and how it's wound onto the printer. It is quite possible you've been trying to print using the wrong side of the ribbon!
4. The Labels Won't Feed Through the Printer Correctly
This is potentially an issue with the sensor that detects the gaps between labels or a registration mark. This might be because the sensor is obstructed or it might just be that it's become quite dirty. A quick clean using a cotton bud or printer wipe should be able to rectify this problem.
Extra Tip: Check the printer driver settings match the label software installed.

5. There is a Grinding Noise when I Print....
This could be a mechanical fault with the machine, part of the machine has become loose or some labels have become stuck underneath the print head. The problem is likely to get worse with time so try to prevent any further printing. We may be able to help you remotely over the phone if it is something straight forward. Failing this we can arrange for a third party engineer to visit your site. Remember - it's always better to seek advice rather than ignoring the problem!
How To Avoid The Problems Above ?!
GOOD HOUSEKEEPING! It's true what they say and prevention is cheaper (and easier) than the cure. The first thing we would always recommend is regular cleaning of the printer and keeping it free of adhesive. This will help prevent a range of issues including label jams and breakdowns. You may also wish to consider a maintenance contract with a printer support company.
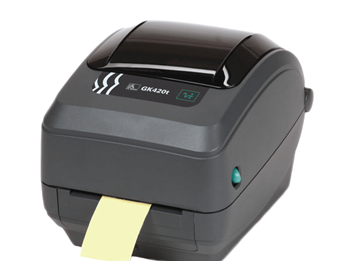
We hope the tips above help and we would always stress good house keeping is the key to preventing most of the issues we come across! Please get in touch though if you are looking for label or ribbon supply to suit these types of printers.